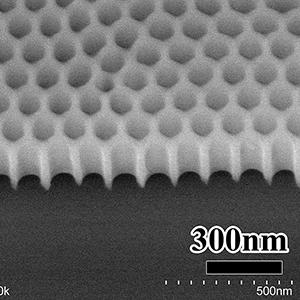
Ultrathin AAO templates have self-organized honeycomb-like nanopores, and they are usually from several ten nanometers to several hundred nanometers in thickness.
Ultrathin AAO templates have been widely used for fabrication of large-scale ordered arrays of surface nanostructures such as nanodots and nanoholes on the surface of substrates. Pores of ultrathin AAO template are uniform in diameter and highly ordered in a short-range. In addition, the material (Al2O3) is transparent in the near-infrared and visible spectrum, and is electrically insulated. Compared to other technology for making ordered nanostructures, ultrathin AAO template has special advantages such as large pattern area (>1 cm^2), high throughput, ultrahigh density (10^8–10&12 cm^2) of the surface nanostructures, and low equipment costs.
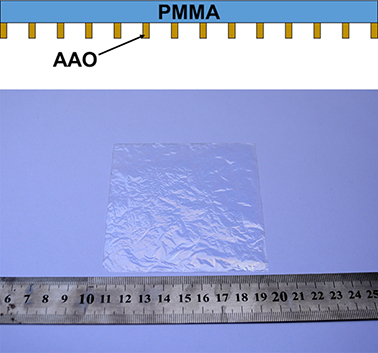
Fig. 1. Up: Schmatic of our ultrathin AAO template product (or AAO membrane); bottom: a photo of large area PMMA/ultrathin AAO template film.

Fig. 2. The product of ultrathin AAO template in standard size (15×15mm).
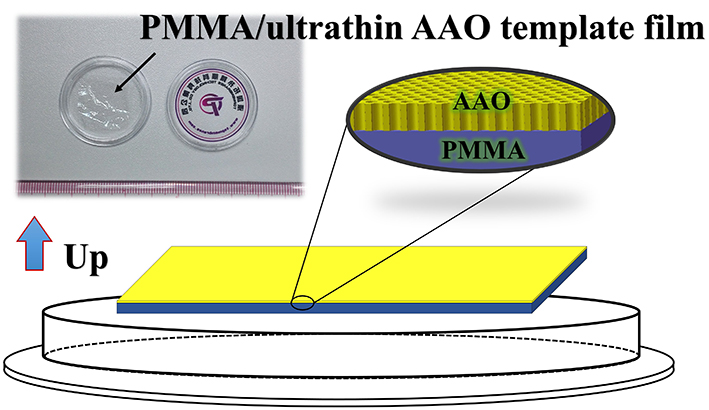
Fig. 3. Schematic of our ultrathin AAO template product in the package.
Because of the small thickness (less than one micron), handling of ultrathin AAO template/membrane is a great challenge. In addition, it is very fragile and inconvenient to use. Here, a layer of Polymethyl methacrylate (PMMA) is coated on the surface of ultrathin AAO template (fig. 1, up) to assist the transfer process. With the assistance of PMMA layer, ultrathin AAO template up to 80cm2 can be easily manipulated (fig. 1, bottom). This technique allows users to carry, cut, or transfer ultrathin AAO template to any substrate easily. A small piece of PMMA/ultrathin AAO template film with typical package is shown in Fig. 2. Typically, PMMA side is at the bottom of the package without further instruction (fig. 3).
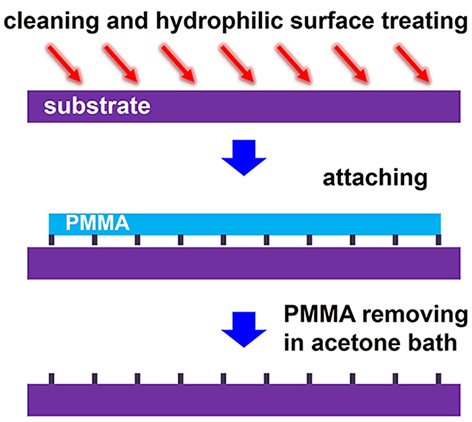
Fig. 4. The schematic of transferring ultrathin AAO template in three steps. Step 1, clean the substrate and treat into slightly hydrophilic; step 2, place the AAO membrane on the substrate with AAO side facing to the substrate; step 3, remove PMMA in acetone bath.
Generally, ultrathin AAO template is used by transferring on the substrates. Fig. 6 illustrates the principle of the process of transferring in three steps. Step 1: clean and hydrophilic treatment. Hydrophilic treatment allows the membrane to be contact with the substrate more tightly. A low power oxygen plasma or ozone plasma could work. Step 2: place the AAO membrane on the substrate. Step 3: removing of PMMA in acetone bath.
Note:
(a) We will tell you the detailed tricks of transferring operation after purchase, or you can download the reference data from:
http://topmembranes.com/intro/UltrathinAAO_en.rar
for English version, and
http://topmembranes.com/intro/Ultrathin_AAO_transfer_cn.rar
for Chinese version.
(b) If hydrophilic treatment is not unavailable, hydrophobic surface is also feasible.
(c) If PMMA side adhere to substrate instead of AAO side in step 2, the front side of AAO membrane will stick to the surface of substrate. Since the front side has a higher roughness, the adhesion between AAO and substrate may be weak, so AAO could be easier removed by tape after experiments.
(d) Don’t touch the surface of ultrathin AAO template after transfer.
(e) We also provide transfer services. The customer can provide specific substrates, or can ask us to provide if we have.
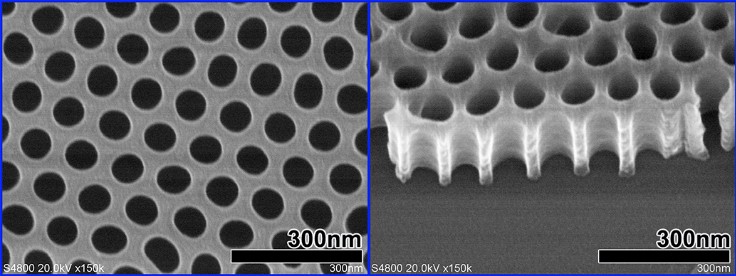
5. Top view (left) and section view (right) of ultrathin AAO template on Si wafer.
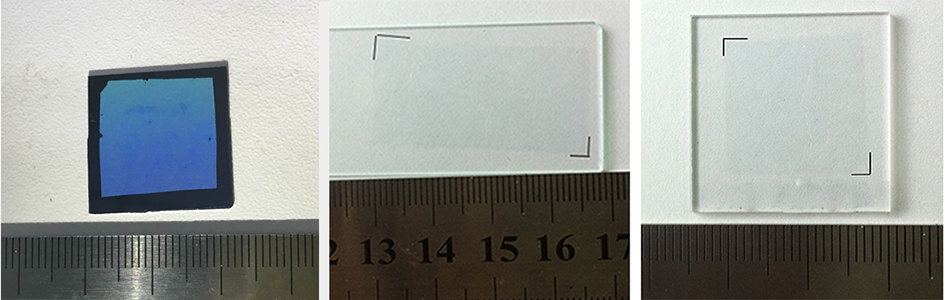
Fig. 6. ultrathin AAO template on silicon (left), glass (middle) and fused silica (right). The interpore distance of the AAO in (a) is about 450nm.
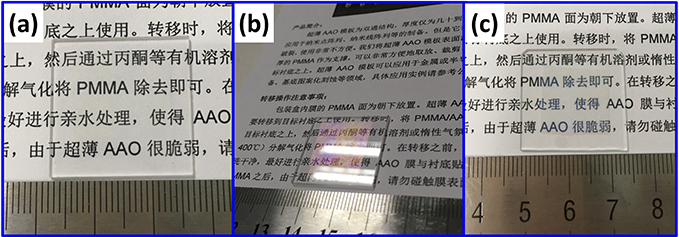
Fig. 7. Ultrathin AAO template on (a,b) silica and (c) glass. The interpore distances of the AAO in (a) and (c) are 100nm and 450nm.
With our transferring technique, AAO template can be transferred onto various substrates, such as silicon, sapphire, fused silica, glass, stainless steel, SiC、ZnO、GaN、ITO、FTO、PDMS、PET, etc. Taking ultrathin AAO template as mask, we can easily make metal or semiconductor nanostructures, including nanoparticle and nanowire arrays. In addition, AAO can be used as masking for etching the substrates.
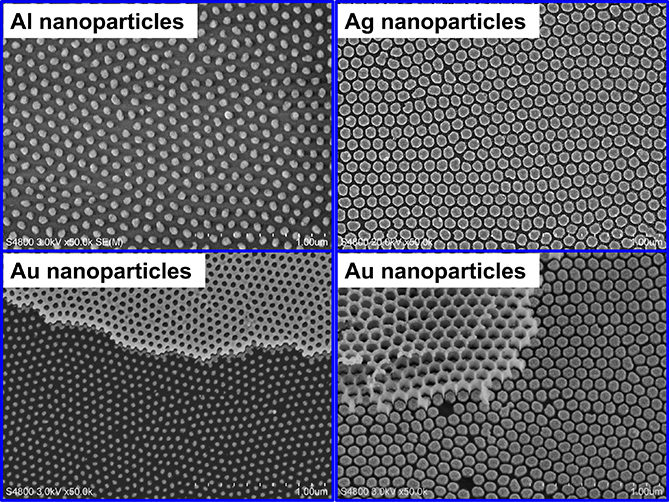
Fig. 8. Metal nanoparticles fabricated by using ultrathin AAO template via E-beam evaporation.
As to the fabrication of nanoparticle arrays on substrates via Physical Vapor Deposition such as electron beam evaporation, ultrathin AAO templates (interpore distance 65 nm, 100 nm, 125nm) with the ratio of pore diameter to AAO thickness between 1:3 and 1:6 are recommended. But for AAO with interpore distance 450 nm, the ratio can be 1:1.
The detailed relationship between nanoparticles and the structures of ultrathin AAO template is shown in the reference Chem. Mater., 2005, 17, 580-585, reported by Yong Lei et al.
Ultrathin AAO template with interpore distance of ~450nm seems light blue. Others are colorless.
You can image the structure with either SEM or AFM. Due to the small thickness, sputtering gold or carbon before SEM test is not necessary, given the substrate is conductive. Ultrathin AAO template can be removed by 5% phosphate acid at 30℃ slowly, or by 5wt.% NaOH at room temperature quickly. Alternatively, the membrane can be removed by Kapton tape.
You can find some typical applications of ultrathin AAO template at:
http://topmembranes.com/en/lmxx.asp?id=26
How to fabricate nanoparticle arrays via ultrathin AAO template:
http://topmembranes.com/en/UploadFiles/file/20160923/20160923163688038803.rar
Up to Date product parameter(Please download here):
http://topmembranes.com/UploadFiles/Product/Ultrathin_AAO.pdf
Interpore distance is the distance between the centers of neighbouring pores.
Keywords: AAO template; Ultrathin AAO template; AAO membrane.