Organic membranes are the most widely used membranes in industrial processes due to their high-packing density, small footprints, and lightweight characters. Among the organic membranes, porous poly(tetrafluoroethylene) (PTFE) membrane exhibits outstanding chemical stability, high heat resistance, strong hydrophobicity, and high fracture toughness due to the strong C-C and C-F bonds and the carbon backbone, which is protected by the uniform helical sheath formed by the electron cloud of the fluorine atoms. These properties make it suitable for a variety of applications, such as exhaust-gas treatment, membrane distillation (MD), osmotic distillation (OD), and oil-water separation.
The requirement for specific membrane properties varies with its targeted application. PTFE membranes were tailored to meet the needs of different membrane applications. In gas-solid separation, the solidparticle rejection rate and gas permeability are the most important parameters of porous membranes. To acquire a good separation performance of the membrane, large pore sizes of ~ 5 μm with a narrow pore-size distribution and thickness below ~ 50 μm are needed. Furthermore, high porosity and specific surface area of PTFE membrane are also required in gas-solid separation. To meet the requirement of the gas-solid separation process, PTFE nanofibers are usually prepared by biaxial stretching and electrospinning to achieve a higher specific surface area, which provides more contact area between the particles and fibers, while retaining sufficient particle retention and gas permeability. Membrane distillation (MD) is a thermally-driven membrane- separation process that is induced by the temperature difference across the hydrophobic membrane. Mass- and thermal-transfer coefficients are the two key parts that determine the efficiency of an MD process. The optimization of both mass and heat transfer in MD depends on the structural and chemical properties of the membrane. In an MD process, PTFE membrane is used for its low thermal conductivity and hydrophobic nature to minimize heat loss. The PTFE also has a low liquid entry pressure and a suitable pore structure for MD. The pore size of PTFE membranes used in MD is usually ~ 0.5 μm. Furthermore, in oil-water separation, the membrane should either be water-repellent (hydrophobic and oleophilic) or oil-repellent (hydrophilic and oleophobic) depending on the feed water-oil mixture (oil-in-water emulsion or water-in-oil emulsion).
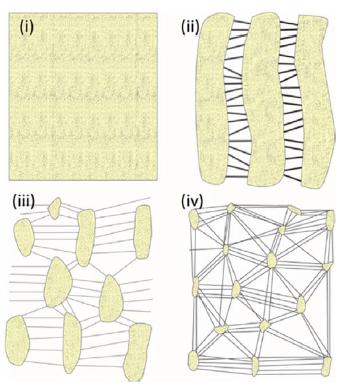
Figure 1. Schematic of PTFE stretching process in different stages: (i)raw PTFE sheet, (ii)early-stage stretching or strip crack process, (iii)node-forming stage or uniaxial tension process, (iv)uniform node connection or biaxial tension process.
1.Membrane distillation
Membrane distillation (MD) is a non-isothermal separation process driven by the vapor pressure difference, induced by the temperature difference across the hydrophobic membrane. It is an environmentally friendly technique aimed at acquiring potable water. Porous PTFE membrane, due to its good thermal stability, chemical resistance, low surface energy, thermal conductivity, and high porosity, is an ideal material for MD. Generally, MD performance is mainly influenced by the membrane pore size, porosity, membrane thickness, surface free energy, and thermal conductivity. These parameters directly influence the mass and thermal transfer of the MD process. Zhang et al. valuated the commercial PTFE flat membrane for desalination of brine water through VMD. The permeate flux and permeate conductivity of different PTFE membranes under different operating conditions were tested and compared. The results showed that the degree of vacuum, feed temperature, and feed flow rate had positive effects on permeate flux. The salt rejections were more than 99.9%, which indicated that the PTFE membranes exhibited satisfying performances for membrane distillation. Flat sheet and hollow fiber PTFE are the most commonly used membranes for MD. Huang et al. fabricated ultrafine fibrous porous PTFE membranes (UFPPM) by sintering electrospun PTFE/PVA composite membranes. The porosity of this membrane is higher than 76%. In VMD (Fig. 2), the permeate flux stabilized at 14.53 L m−2 h−1, and the salt rejections were maintained above 99.8% after operation for 35 h. The long-term operation of the UFPPM in VMD indicates that these membranes have excellent stability in harsh-water-desalination experiments.
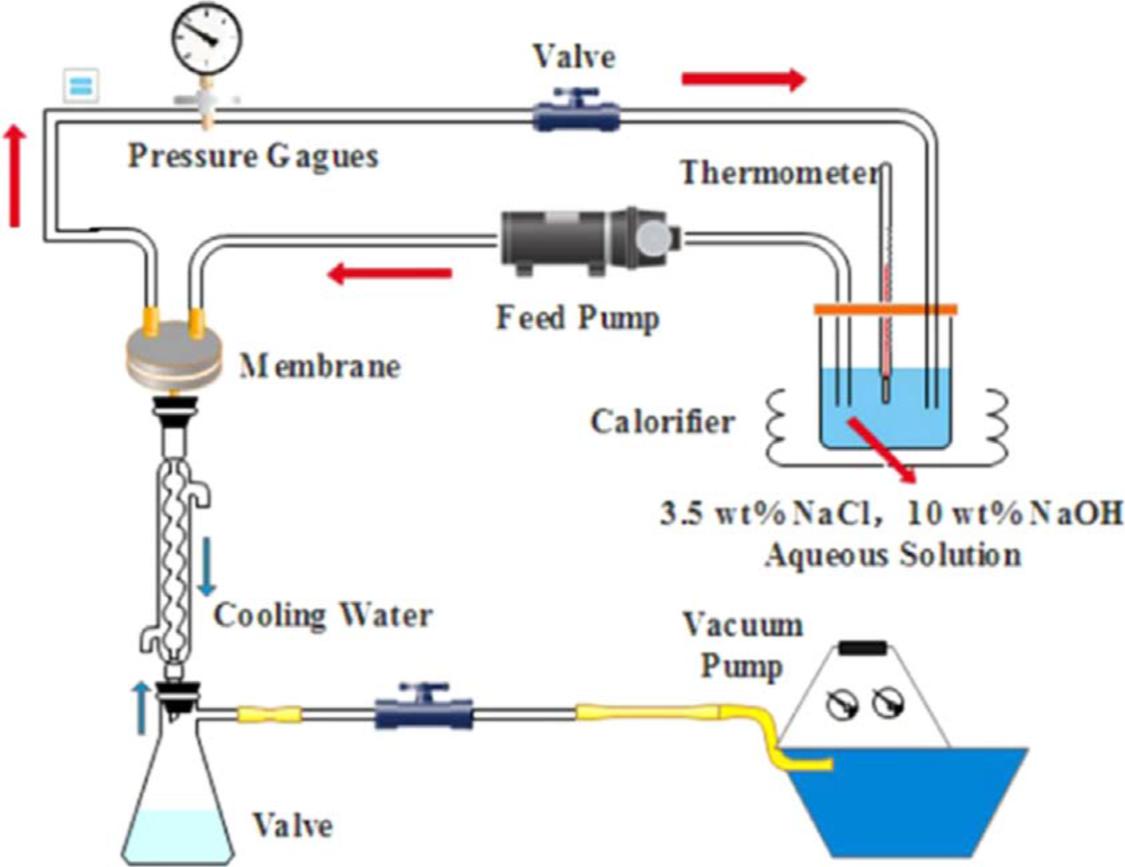
Figure 2. Schematic of the experimental VMD apparatus
2.Oil-water separation
Many industrial processes including oil drilling and tertiary oil extraction can generate oil-bearing wastewater that is difficult to remove using traditional methods. Membrane material with enhanced surface properties, such as superhydrophobicity and superoleophilicity, superhydrophilicity, and underwater superoleophobicity, are suitable for oil/water separation. The pore size of the membrane used in oil/water separation is usually approximately ~ 0.2 μm. Hu et al. compared the oil/water separation performance of PTFE, PVDF, and nitrocellulose in a cross-flow microfiltration process. In all cases there is a decline in flux with time that is associated with the initial formation of the emulsion “cake” layer. This phenomenon can be attributed to the oleophilicity of the membrane. Higher temperature, filtration velocity, and trans-membrane pressure are desirable for higher flux. To improve the hydrophilicity and anti-fouling property of the PTFE flat membrane, Xue et al. developed a facile method to modify the membrane via the co-deposition of catechol (CA) and polyethyleneimine (PEI) followed by surface mineralization of γ-(2,3-epoxypropoxy) propytrimethoxysilane (KH560). The as-prepared hydrophilized PTFE flat membranes possess an excellent oil-resistant ability with an oil rejection ratio close to 99%. This underwater oleophobic membrane prevented the formation of emulsion cake on the surface of the membrane.
3.Air purification
PTFE membrane filters are often used to control particulate matters in various industries. Their uniform pore structure with node-connected nanofibrils and low fraction factor make it possible to achieve remarkable filtration performance. Zhong et al. reported a ZnO nanorod functionalized PTFE membrane for fine dust filtration. A barrier-like hierarchical structure was constructed by hydrothermally growing a layer of ZnO nanorods, which can uniformly wrap around the nanofibrils of the PTFE. The dust filtration results shown that the fineparticle rejection was greater than 99.9999%. The pressure drop was 40% lower than that without ZnO nanorods. Feng et al. prepared an amphiphobic PTFE membrane for oil aerosol removal, in which low-surface-free-energy monomers were grafted onto the ZnOnanoparticle-wrapped PTFE nanofibrils. This porous amphiphobic PTFE membrane exhibited good performance in oil aerosol filtration with a fine-particle-rejection rate of 99.5%. The operational pressure drop was less than 0.5 kPa. In addition, functionalization of the membrane with gas pollutant degradation performance is also a promising direction for this material. Feng et al. further deposited a layer of Ag nanoparticles on the ZnO nanorods, which showed a 60% formaldehyde degradation rate.
4.Other applications
Apart from the above-mentioned applications of porous PTFE membrane, PTFE membrane is also suitable for fuel cell, CO2 capture, gas/vapor separation and solvent filtration]. For a proton exchange membrane fuel cell, a hydrophobic PTFE with good mechanical strength is usually needed in order to improve the interface compatibility, reduce the areal resistance, and increase the output performance of a single cell. In addition, good ionic conductivity is another key criterion for fuel cell membrane. Benipal et al. used porous PTFE thin film as a separator between the anode and cathode in direct glycerol fuel cell (DGFC). The effect of pore size, thickness, and some other related properties were investigated. The higher pore size of 1.0 μm possesses a 46.9% higher peak power density than that of 0.22μm. In addition, the internal resistance of the DGFC with a PTFE thin film with a pore size of 0.22μm was 62.9% higher than that of a PTFE thin film with a pore size of 1.0μm. This is because the thickness would influence the performance, which is measured by the Ohmic resistance and fuel crossover effect. Tang et al. reported a PTFE hollow fiber membrane used in CO2 capture. The PTFE polymer maintained good stability in the absorbent solutions over 24 wks. The surface hydrophobicity did not decrease during long-term immersion. Constantinous et al. investigated the CO2 absorption in amine solutions with a flat PTFE membrane microstructured contactor. The results showed monoethanolamine (MEA) solution absorbed more CO2 (19% of CO2 was absorbed in 0.16 s) than diethanolamine (DEA) (14% of CO2 was absorbed in 0.16 s).