According to the membrane separation technology exchange Wechat Public Platform October 9, 2016, the synthetic process of drug molecules is multi-step reaction. Because of the solubility and boiling characteristics of different pharmaceutical intermediates in the synthesis process, and the need for reaction conditions, it often involves a variety of solvents and catalysts, as well as the accompanying process of filtration, drying, rotary evaporation, extraction, crystallization and so on, which is time-consuming and laborious. The continuous production process can reduce the operation steps and save 10-20% of the cost. However, the continuous preparation of multi-step reactions is not so convenient to optimize: the compatibility of the front and back steps, different temperature conditions, different reaction solvents, side reactions of catalysts and so on all limit the optimization.
The membrane process is suitable for continuous preparation because of its convenient operation and no phase transition process. Organic solvent nanofiltration (OSN) can be used in solvent exchange and catalyst recovery processes.
The team of Professor Andrew Livingston of Imperial College of Technology completed the continuous consecutive reactions of catalyst recovery and solvent exchange using membrane separation process for the first time, and published Angew. Chem, Continuous Consecutive Reactions with Inter-Reaction Solvent Exchange by Membrane Separation. Int. Ed. 2016, 55, 1-5, DOI: 10.1002/anie.201607795).
Organic nanofiltration membranes are one of the hotspots in membrane science. Professor Andrew Livingston's team has been a pioneer in this field. For the first time, they tried to introduce membrane process into the above reaction process. Compared with distillation, membrane process has been known for its low energy consumption and low operating temperature. In this study, they chose a typical high boiling point solvent for a low boiling point solvent - 6-chloro-2-(4-chlorobenzoyl) - 1H-indole-3-acetic acid (a typical COX2 inhibitor) synthesis process. The first step needs to be carried out in DMF, while the second step needs to be carried out in ethanol.
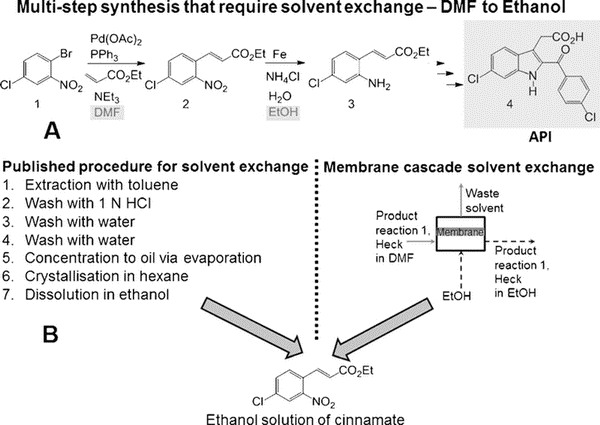
The reaction is 6- chloro -2- (4- Chlorobenzoyl) -1H- indole -3- acetic acid preparation process. As shown in Figure A above, the original reaction consists of seven steps (toluene extraction, hydrochloric acid cleaning, washing, washing, evaporation concentration, ethane crystallization, ethanol dissolution), involving the exchange of solvent DMF and ethanol. The membrane process can now be optimized into one step, as shown in Figure B above, and in more detail as shown in the following figure. It consists of three membrane separation units, each of which has a circulation process, and the flow rate is controlled by multiple pumps.
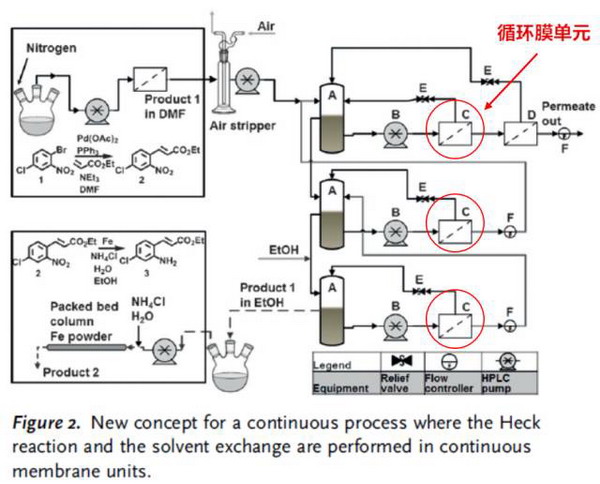
The reaction lasted 160 hours and the solvent was replaced by 82% ethanol from 100% DMF. The product was diluted 2.1 times and the yield was over 95%. The concentration of catalyst palladium in the osmotic solution was within the expected range (less than 10% in the membrane reactor, less than 100 ppm). Although palladium contamination in the product is still high and needs further purification, the content is still twice as low as the original step.
In the support information, we can find out the method of making the membrane: dissolve VESTAKEEP 4000P into PEEK by water, prepare the membrane solution with 12% solid content, and dry at 120 C to prepare the membrane.
On the tolerance of membrane reactors. The team used 0.05 to 1mol% catalyst for 1100 hours of operation. The state of the membrane reactor is stable, and the rejection rate of the catalyst is about 90%. However, the tolerance of other components, such as expansion of HPLC pumps and plastics, remains to be improved.