According to Sohu Public Platform January 13, 2017, recently, the Bass Advanced Separation Engineering Center (CASE) scientists are predicting the development of 3D printing and advanced membrane engineering. It is understood that membranes are semipermeable selective barriers that separate gas or liquid molecules into two streams. A common example is reverse osmosis membranes, which separate salt from water.
In a new article published in the Journal of Membrane Science, CASE researchers noted several limitations that currently exist in membrane engineering. Due to the limitation of current manufacturing technology, membranes are mainly confined to tubular / hollow fibers and flat surface drawings. Therefore, the membranes we can make today are relatively inaccurate, which limits how we can successfully separate different properties.
For the first time, this paper provides a compelling example of 3D printing technology as a new means of creating more advanced membranes. The CASE team found that 3D printing provides new technologies for producing films of different shapes, types and designs that can be designed, manufactured and controlled more accurately than ever before.
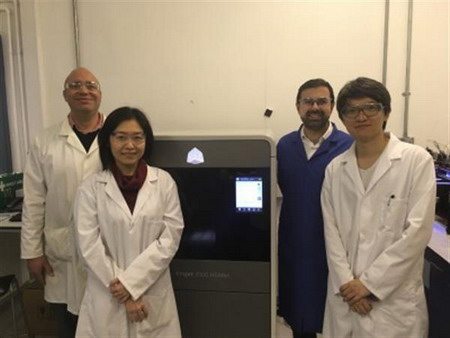
CASE Director Dr Darrell Patterson said: "This is the first time that the possibility and challenge of producing separation membranes with 3D printing have been explored.
"Although 3D printing technology is not developed enough to mass-produce films, it is cost-competitive compared with existing products," Patterson explained. "This work demonstrates the possibilities of future 3D printing: the production of films now has access to complex pore structures including controlled, integrated surface patterns and natural-based films."
According to CASE innovations, 3D printing can be an ideal designer hole and surface shape for engineering new films that enhance microscopic mixing and shear flow across membrane surfaces. As a result, the time required for cleaning up and the scaling of membranes can be greatly reduced.
The use of 3D printing could in turn lead to more sustainable molecular separation and reduced energy use in areas such as the water industry.
CASE research is a welcome project as industries around the world want to set a more environmentally friendly future. Currently, up to 15% of the energy used worldwide comes from industrial products such as the separation and purification of gases, fine chemicals and freshwater. The separation process also accounts for 40% to 70% of industrial and operating costs.
On the other hand, the innovation of membrane technology may provide lower energy and more sustainable molecular separation, which has a wide range of applications in separating liquids and gases. With these advances, 3D printing can reduce our industrial carbon footprint.